Die Casting Machining: The Essential Guide for Metal Fabricators
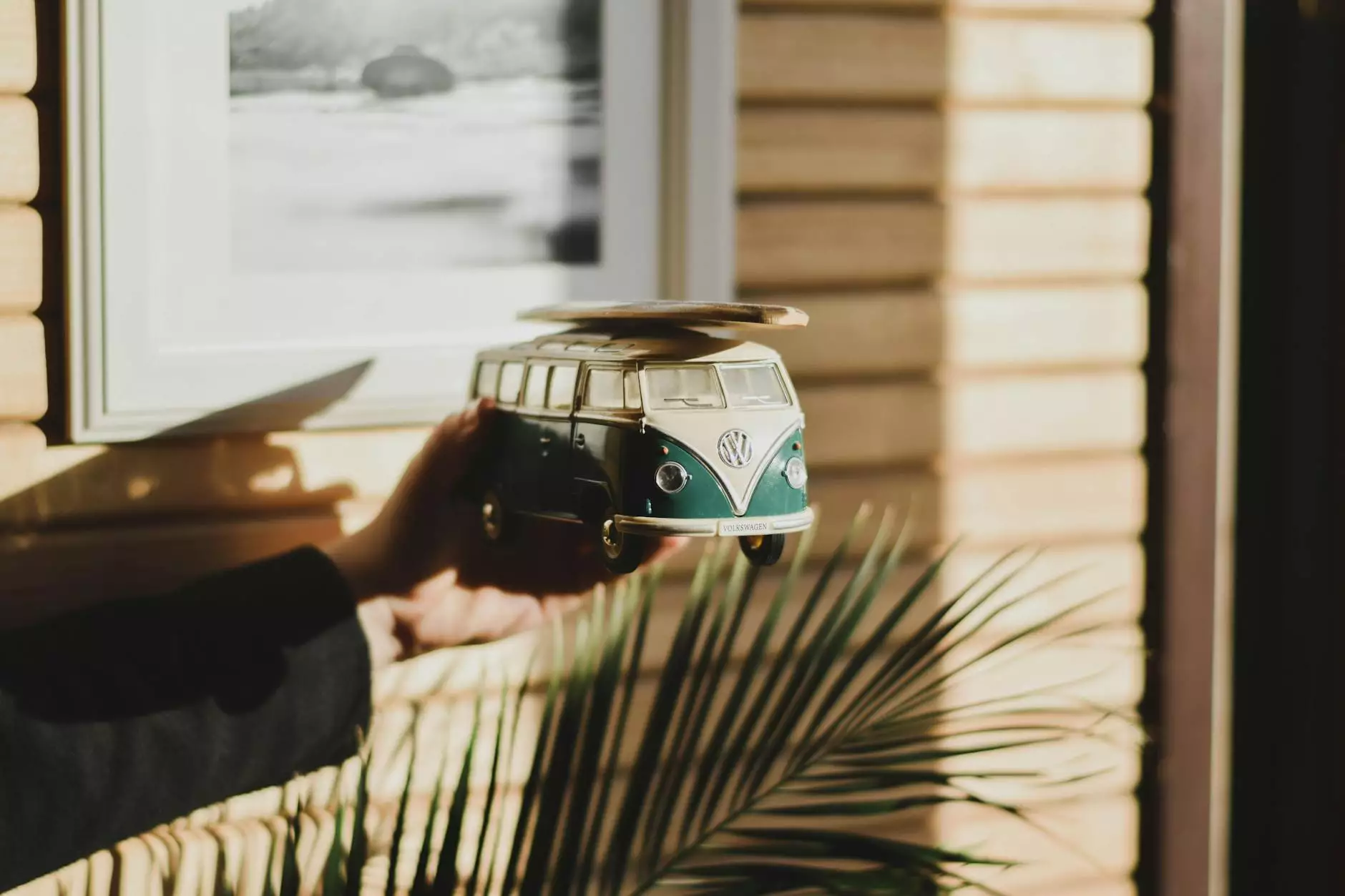
Die casting machining is a pivotal process in the world of metal fabrication, offering unparalleled precision and efficiency in producing complex metal parts. As a core technique in manufacturing, it combines the art of metallurgy with advanced engineering to meet the demanding needs of various industries. This comprehensive guide will delve into the intricacies of die casting machining, its benefits, applications, and future trends that metal fabricators must consider to thrive in a competitive marketplace.
What is Die Casting Machining?
Die casting machining is a manufacturing process that involves forcing molten metal into a mold cavity under high pressure. The mold, often called a die, hardens rapidly, enabling the production of intricate shapes with smooth surfaces and tight tolerances. This technique is primarily used for non-ferrous metals, including aluminum, zinc, and magnesium, to create parts that are durable and lightweight.
The Die Casting Process Explained
The die casting process can be broken down into several key stages:
- Mold Preparation: The die is created using advanced machining techniques. It is extremely precise and designed to meet the exact specifications required for the final product.
- Metal Melting: Selected metal alloys are melted in a furnace to achieve the desired consistency.
- Injection: The molten metal is injected into the die at high speeds, filling the mold cavity completely.
- Cooling: The metal cools and solidifies quickly, taking the shape of the die.
- Unloading: Once the part is solidified, the die is opened to retrieve the finished product.
The Advantages of Die Casting Machining
Choosing die casting machining for your manufacturing needs offers numerous benefits. Here are some of the most compelling advantages:
- High Dimensional Accuracy: The precision of die casting ensures each part meets tight tolerances, reducing the need for extensive machining.
- Consistency: Automated processes lead to uniform products, minimizing variations in production batches.
- Cost-Effective for Large Volumes: While tooling costs can be high, the efficiency of die casting leads to lower per-unit costs in large production runs.
- Complex Geometries: The ability to produce intricate designs is one of the key benefits, making it suitable for complex components.
- Material Efficiency: Minimal wastage of the initial metal due to the closed-loop process allows for better resource utilization.
Materials Used in Die Casting
Die casting can be performed using a variety of metals, but the most common materials include:
- Aluminum: Lightweight, corrosion-resistant, and excellent thermal conductivity make aluminum an ideal choice for automotive and aerospace applications.
- Zinc: Known for its strength and durability, zinc die casting provides high dimensional accuracy and is often used for small, complex parts.
- Magnesium: The lightest structural metal, magnesium is gaining popularity for applications requiring reduced weight, especially in the automotive sector.
Applications of Die Casting Machining
The versatility of die casting machining means it is widely used across various industries. Some notable applications include:
- Automotive Industry: Engine components, transmission housings, and structural parts benefit from the strength and weight efficiency provided by die casting.
- Aerospace: Critical aerospace parts are produced with precise tolerances to ensure safety and performance.
- Electronics: Die casting is used to manufacture housing for electronic devices, providing durability while maintaining a sleek appearance.
- Consumer Goods: Many everyday products, from appliances to furniture, utilize die casting for aesthetic components without compromising functionality.
Die Casting Techniques
There are primarily two methods of die casting machining: hot chamber die casting and cold chamber die casting. Each technique has its specific applications based on the type of metal and part requirements.
Hot Chamber Die Casting
This method is used for metals with low melting points, such as zinc and magnesium. In hot chamber die casting, the melting furnace is directly attached to the die casting machine, which aids in rapid production cycles. This technique enhances productivity, making it ideal for large-volume production of smaller parts.
Cold Chamber Die Casting
Cold chamber die casting is designed for metals with higher melting points, like aluminum. The molten metal is poured into the chamber before being injected into the die. This method is generally slower than hot chamber die casting but is essential for producing robust parts designed to endure higher stresses.
Quality Control in Die Casting Machining
Ensuring the quality of die cast products is paramount. Implementing rigorous quality control protocols can significantly enhance the reliability of produced parts. Some key measures include:
- Visual Inspection: Regular checks for surface defects and dimensional accuracy should be carried out to meet industry standards.
- Testing for Mechanical Properties: Testing samples for tensile strength, hardness, and fatigue resistance can ensure the parts perform as expected under operational conditions.
- Dimensional Measurement: Utilizing advanced measurement tools like CMM (Coordinate Measuring Machines) provides precise dimensional assessment.
Future Trends in Die Casting Machining
The die casting industry is evolving, influenced by technological advancements and market demands. Key trends to watch include:
- Increased Automation: Advanced robotics and AI-driven systems are streamlining the die casting process, enhancing productivity while reducing labor costs.
- 3D Printing Integration: The convergence of 3D printing and die casting allows for rapid prototyping and shorter lead times for tooling.
- Sustainability Practices: Environmentally-friendly materials and energy-efficient processes are becoming essential as businesses focus on reducing their carbon footprint.
Conclusion
In summary, die casting machining is a cornerstone of modern manufacturing, particularly for businesses operating within the realm of metal fabrication. With its numerous advantages including precision, speed, and material efficiency, it is a process that can significantly boost production capabilities and reduce costs. As trends evolve and new technologies emerge, staying informed about the latest advancements will empower metal fabricators to adapt and thrive in an ever-changing marketplace.
For industries looking to harness the power of die casting, deepmould.net stands ready to offer cutting-edge solutions tailored to meet your needs. Partnering with experienced metal fabricators can unlock new potential and drive your business forward into the future.