Exploring Plastic Mold Tooling: A Catalyst for Success in Metal Fabrication
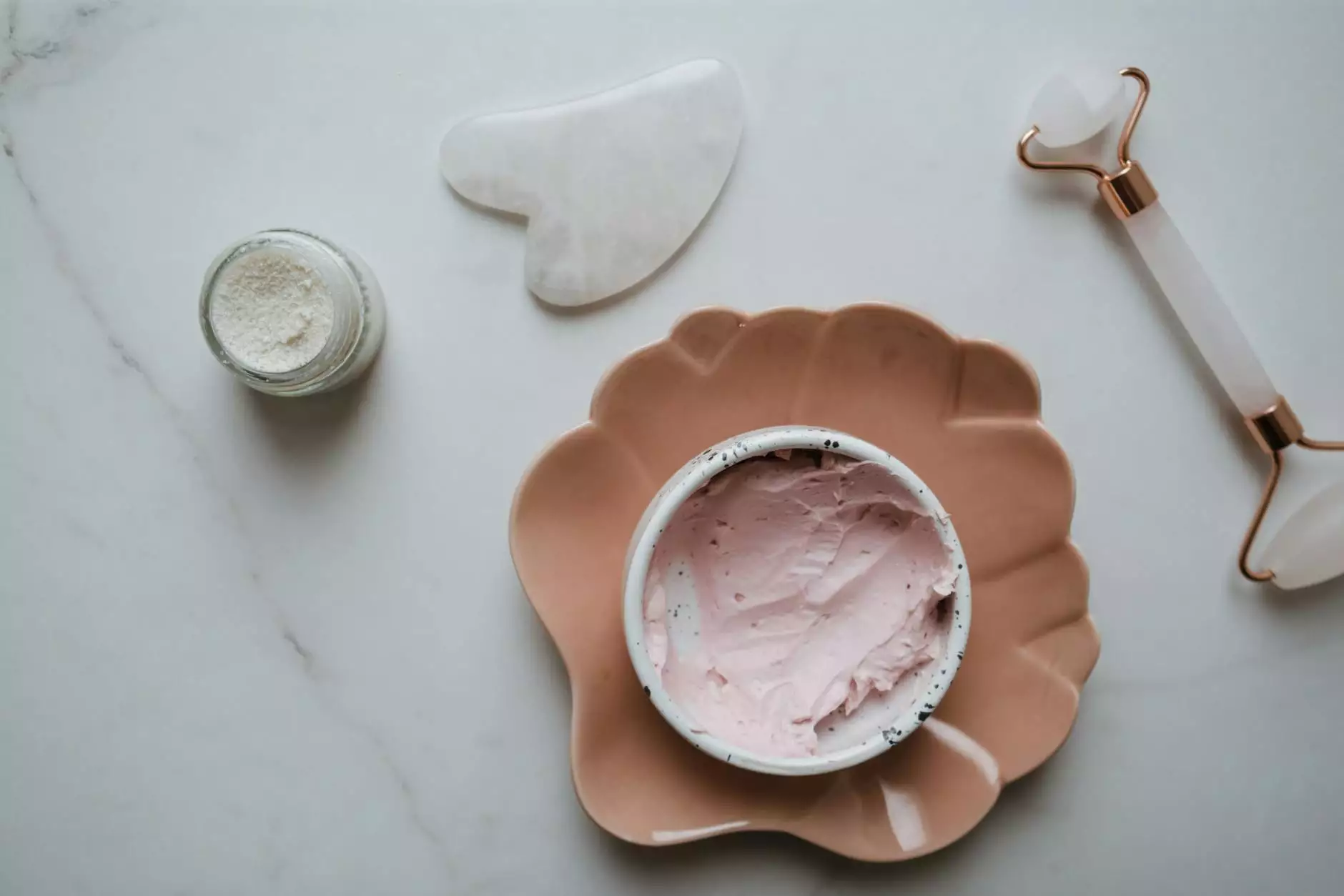
Plastic mold tooling is a pivotal aspect of the manufacturing sector, particularly in metal fabrication. As businesses continue to seek innovative ways to enhance efficiency and reduce production costs, understanding the essentials of this process becomes increasingly important. This article delves deep into the world of plastic mold tooling, its significance, applications, and the implications it holds for the manufacturing industry, especially for companies like DeepMould.net.
What is Plastic Mold Tooling?
At its core, plastic mold tooling refers to the creation of molds that are used to shape plastic materials into specific forms. These molds are essential for producing high-quality plastic parts that are consistent and precise in shape and size. Advanced techniques in plastic mold tooling allow manufacturers to create complex parts that would be nearly impossible to achieve through other manufacturing processes.
The Importance of Plastic Mold Tooling in Metal Fabrication
The integration of plastic mold tooling in metal fabrication brings forth several critical benefits:
- Enhanced Precision: Molds created through meticulous tooling ensure that every piece produced meets rigorous standards of accuracy.
- Cost-Effectiveness: Reducing waste through efficient mold design helps in minimizing material costs, ultimately driving down production expenses.
- Scalability: Once a mold is perfected, it can be replicated for mass production, allowing businesses to scale operations without sacrificing quality.
- Design Flexibility: Mold tooling allows for a vast array of designs, enabling innovation and customization within product lines.
Key Components of Plastic Mold Tooling
To realize the full potential of plastic mold tooling, understanding its key components is essential. Here are the fundamental elements involved in the process:
Mold Design
The design of the mold is critical, as it dictates the final product's characteristics. Effective mold design takes into consideration aspects such as:
- Part geometry
- Material selection
- Production volume
Mold Materials
The materials used for mold creation affect durability and performance. Common materials include:
- Steel: Known for its strength and longevity.
- Aluminum: Offers lightweight characteristics and is suitable for low-volume production.
- Composite Materials: Used for specific applications that require additional properties like corrosion resistance.
Mold Manufacturing Processes
Different manufacturing processes are employed in producing molds, including:
- Computer Numerical Control (CNC) Machining: Ensures precision in mold creation by using automated tools.
- Spark Erosion: Useful for intricate designs where standard machining falls short.
- 3D Printing: Provides rapid prototyping and the ability to create complex structures with minimal material waste.
The Role of Plastic Mold Tooling in Metal Fabrication
Within the realm of metal fabrication, plastic mold tooling plays a crucial role. It enhances various operations, enabling manufacturers to:
- Fabricate parts that require precision in metal components using plastic molds.
- Integrate plastic elements into metal parts for hybrid applications, enhancing functionality.
- Reduce machining time by pre-shaping components through molding processes.
Benefits of Utilizing Plastic Mold Tooling
Investing in plastic mold tooling offers several advantages, which can significantly benefit both manufacturers and end consumers:
Improved Product Quality
One of the most significant benefits is the enhancement of product quality. Molds designed with precision guarantee that every part meets specifications, reducing defects and rework.
Faster Production Times
Adopting efficient tooling procedures can drastically decrease production times, giving businesses the agility they need to meet market demands promptly.
Lower Material Costs
Through the optimization of mold design and usage, manufacturers can minimize material waste, resulting in lower costs.
Challenges in Plastic Mold Tooling
While there are numerous benefits to plastic mold tooling, certain challenges must be addressed:
Initial Setup Costs
The initial investment required for designing and producing molds can be substantial, which may be a barrier for smaller businesses.
Maintenance and Wear
Molds require regular maintenance to ensure they perform effectively over time. Wear and tear can affect the quality of production.
Technological Advancements
Keeping up with technological changes in mold design and production can be challenging but is necessary to remain competitive.
Innovations in Plastic Mold Tooling
The field of plastic mold tooling is continually evolving, driven by technological advancements. Some notable innovations include:
- Digital Twin Technology: Allows manufacturers to create exact replicas of their molds, facilitating better monitoring and optimization.
- Advanced Material Science: New composite materials provide enhanced performance and durability for molds.
- Artificial Intelligence: AI-driven analytics are proving valuable in optimizing design processes and predictive maintenance.
The Future of Plastic Mold Tooling in Metal Fabrication
As industries evolve, the importance of plastic mold tooling will continue to grow. The future promises:
- Increased automation within the tooling processes.
- Greater focus on sustainability through eco-friendly materials and practices.
- Enhanced customization and flexibility to meet specific client needs.
Conclusion
In summary, understanding plastic mold tooling is imperative for any business involved in metal fabrication. The advantages it delivers in terms of precision, cost-effectiveness, and production efficiency underpin its significant role in modern manufacturing.
As companies like DeepMould.net embrace advancements in plastic mold tooling, they equip themselves to meet the growing demands of the market, fostering innovation and excellence in their respective fields.
Take Action: Enhance Your Manufacturing Processes
If your business is ready to realize the benefits of effective plastic mold tooling, it's time to take action. Evaluate your current manufacturing processes, invest in quality mold design, and explore innovative tools available today to ensure your competitiveness in the market.
For more detailed information and professional services, visit DeepMould.net and take the first step toward enhancing your production capabilities.