CNC Precision Machining Factories: Revolutionizing Metal Fabrication
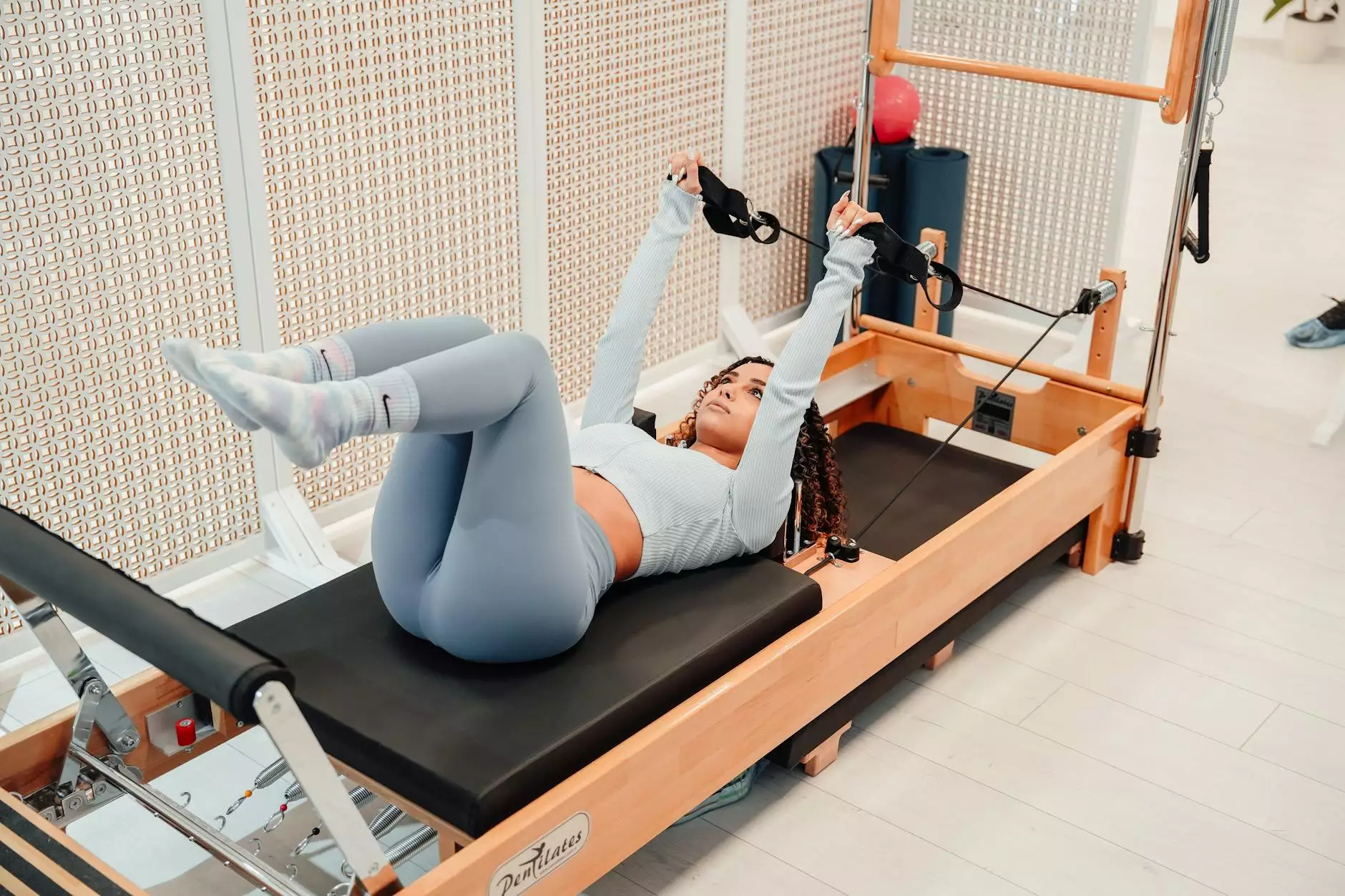
CNC precision machining factories are at the forefront of manufacturing excellence, propelling innovation in the metal fabrication industry. With the rise of advanced technologies and increasing demands for higher precision components, these factories play a crucial role in meeting the needs of various sectors, including aerospace, automotive, and electronics.
What is CNC Machining?
To understand the importance of cnc precision machining factories, we must first grasp the concept of CNC machining itself. CNC, or Computer Numerical Control, refers to the automated control of machining tools by means of a computer. The process involves generating a computer-aided design (CAD) that is then translated into a series of precise movements and operations performed by the CNC machine.
Key Benefits of CNC Precision Machining
The advantages of utilizing cnc precision machining are numerous:
- High Precision: CNC machines can produce components with tolerances as tight as ±0.002mm, ensuring unparalleled accuracy.
- Consistency: Once a program is written, CNC machining can replicate the same part thousands of times without variation.
- Efficiency: Automation allows for quicker production times as machines can operate continuously with minimal supervision.
- Complex Shapes: CNC machines can create intricate shapes that would be impossible to achieve with manual machining.
- Material Versatility: These machines can work with a variety of materials, including metals, plastics, and composites.
The CNC Machining Process
The cnc precision machining process typically involves several stages, which are crucial for producing high-quality parts:
- Design & Programming: Engineers create a detailed CAD model of the component and generate a corresponding CNC program using Computer-Aided Manufacturing (CAM) software.
- Setup: The CNC machine is prepared by installing the necessary tool and securing the raw material in place.
- Machining: The machine executes the program, moving along the predefined paths to cut, drill, and shape the material into the desired form.
- Quality Control: After machining, parts are inspected using precision measuring tools to ensure they meet specifications.
- Finishing: This final step may include processes like polishing, anodizing, or coating to enhance the aesthetic and physical properties of the part.
Applications of CNC Precision Machining
The application of CNC precision machining is vast and varied, touching countless industries and serving multiple purposes. Here are some key applications:
- Aerospace Components: CNC machining is vital for producing lightweight, high-strength components such as aircraft frames and engine parts.
- Automotive Parts: From engine blocks to custom fittings, the automotive industry relies heavily on precision machining for performance and safety.
- Medical Devices: Surgeons require surgical tools and implants that are precision-engineered for safety and effectiveness, attainable through CNC technology.
- Electronics: Components like circuit boards and casings demand accuracy in very small tolerances, making CNC machining indispensable.
Challenges Faced by CNC Precision Machining Factories
Despite their advantages, cnc precision machining factories face several challenges in an evolving marketplace:
- High Initial Investment: The cost of CNC machines and the necessary technology can be prohibitive for small manufacturers.
- Skilled Workforce Required: Programming and maintaining CNC machinery require skilled professionals, demanding a focus on workforce development.
- Market Fluctuations: Changes in demand can lead to production inefficiencies and underutilization of machinery.
- Supply Chain Issues: Accessing high-quality raw materials can be a challenge, affecting production schedules and quality.
The Future of CNC Precision Machining
The future of cnc precision machining factories looks promising, driven by technological advancements and an increasing demand for precision:
- Automation and AI: The integration of artificial intelligence and automation will further enhance efficiency and precision in the manufacturing process.
- 3D Printing Integration: The fusion of CNC machining with additive manufacturing techniques will pave the way for innovative production methods.
- Sustainability: Industries are focusing on reducing waste and energy consumption, leading to greener machining practices.
- Customization: The rise of on-demand products necessitates greater flexibility and customization options in CNC machining.
Conclusion
In conclusion, cnc precision machining factories represent the pinnacle of technology and efficiency in the metal fabrication industry. Their ability to produce high-quality, complex components quickly and reliably makes them an invaluable asset across various sectors. As we move forward, the synergy of advanced technologies, skilled labor, and innovative practices will ensure that these factories not only meet but exceed the growing demands of tomorrow's markets.
For businesses looking to leverage the benefits of cnc precision machining, partnering with a skilled and reputable factory is crucial. At deepmould.net, we are committed to delivering excellence in metal fabrication through our state-of-the-art CNC machining processes. Let us help you navigate the complexities of creation and achieve the precision that sets your products apart in the marketplace.