Exploring CNC Lathe Machining: Insights from a Leading China CNC Lathe Machining Supplier
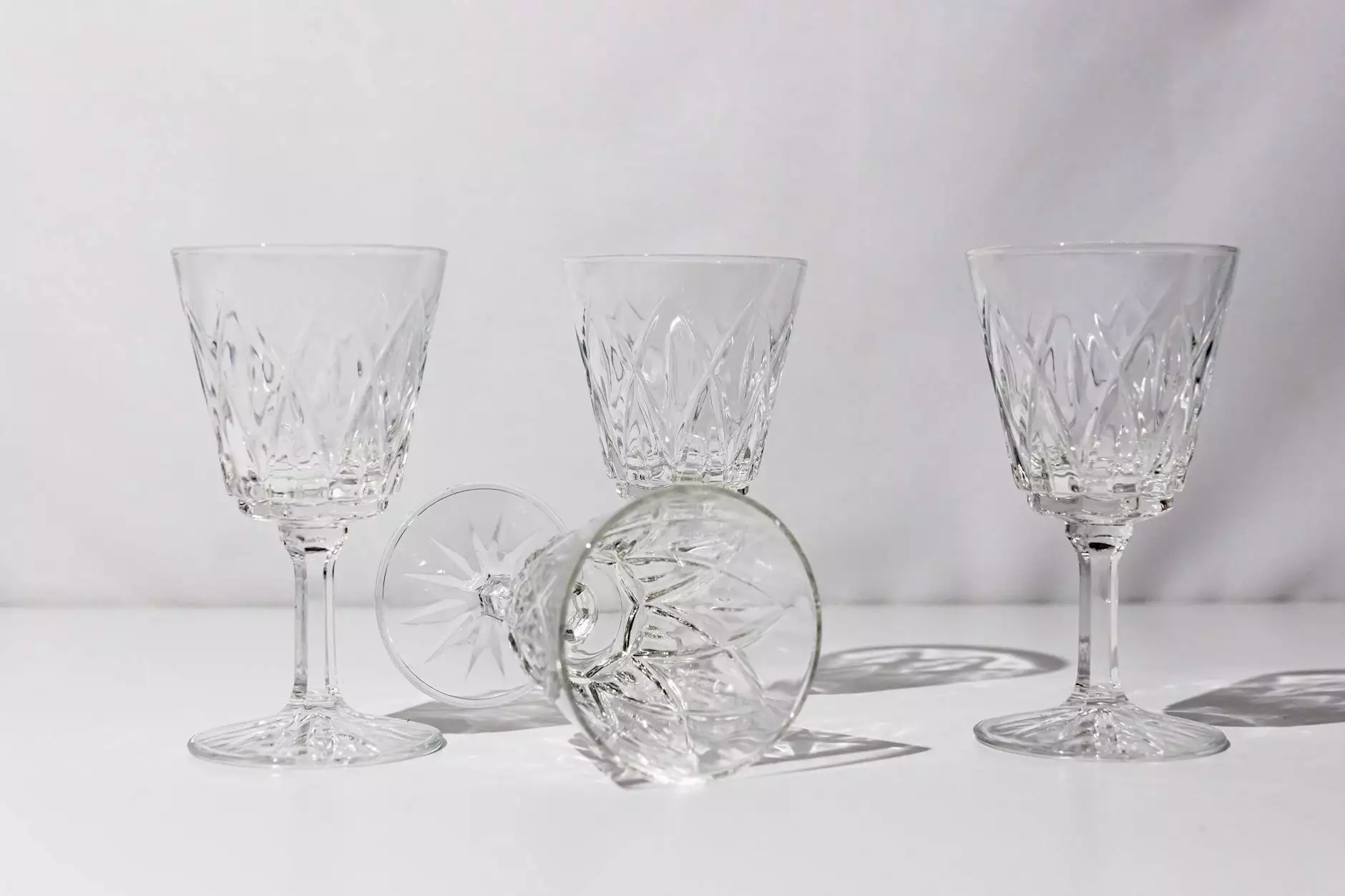
CNC lathe machining is an indispensable part of modern manufacturing, especially for metal fabricators looking for precision, efficiency, and scalability. As a prominent China CNC lathe machining supplier, our goal is to provide a deep understanding of this technology, its applications, and the standards that ensure quality outcomes for businesses around the globe.
The Basics of CNC Lathe Machining
Computer Numerical Control (CNC) machining has revolutionized the manufacturing sector. In CNC lathe machining, a computer executes precise movements of a cutting tool against a rotating workpiece. This method allows for high accuracy and the ability to produce complex parts with repeatable results.
Key Components of CNC Lathe Machines
- Control Unit: This is the brain of the CNC machine, interpreting programmed commands into machine movement.
- Spindle: The spindle holds and rotates the workpiece, allowing for uniform cutting.
- Cross Slide: Adjusts the position of the tool post for various machining operations.
- Tool Holder: Secures the cutting tools and can accommodate various types of tools for diverse functions.
- Bed: The structure that supports the machine components, essential for stability and accuracy.
Applications of CNC Lathe Machining in Metal Fabrication
CNC lathe machining has numerous applications in metal fabrication. Here, we explore some of the key industries that benefit from this technology:
1. Automotive Industry
The automotive sector relies heavily on CNC lathe machining for producing precision components such as shafts, gears, and brackets. The ability to manufacture parts with high precision is essential to meet stringent safety and performance regulations.
2. Aerospace Industry
In aerospace, components must withstand extreme conditions. CNC lathe machining allows for the production of lightweight yet strong parts, such as turbine blades and structural components, ensuring compliance with rigorous standards.
3. Medical Devices
Medical manufacturing demands the highest levels of precision. CNC lathes create intricate parts for devices such as surgical instruments and implants, guaranteeing reliability and safety.
4. Electronics
In the electronics industry, CNC machining is vital for crafting components like casings, connectors, and other small, precise parts that must meet strict tolerances.
Benefits of Partnering with a China CNC Lathe Machining Supplier
Teaming up with a quality China CNC lathe machining supplier offers substantial advantages:
Cost-Effectiveness
China is recognized for its production capabilities, allowing manufacturers to achieve lower costs through economies of scale and competitive labor rates. This advantage translates into cost savings for companies abroad.
Access to Advanced Technology
Suppliers in China often invest heavily in the latest machining technology. This means access to cutting-edge CNC machines that provide enhanced capabilities, such as multi-axis machining and automation, which improves efficiency and reduces turnaround times.
Quality Assurance
Leading CNC lathe machining suppliers adhere to international quality standards, including ISO certifications. They implement stringent quality control measures to ensure that all parts meet precise specifications and industry requirements.
Flexible Production Capabilities
Whether you need low-volume prototyping or high-volume production runs, a reliable supplier can adapt to your specific needs, offering configurations that suit all production scales.
Choosing the Right China CNC Lathe Machining Supplier
Finding the perfect partner can be challenging. Here are crucial factors to consider when selecting a China CNC lathe machining supplier:
1. Expertise and Experience
Investigate the supplier's background. An experienced company will better understand the nuances of various industries and machining requirements.
2. Technology and Equipment
Ensure that the supplier utilizes advanced CNC machines and adheres to the latest technological trends. This will guarantee that you receive high-quality products made with precision.
3. Quality Control Processes
Look for suppliers with robust quality control measures to ensure that every product meets the required specifications. This includes inspections, material certifications, and compliance with international standards.
4. Customer Support and Communication
Efficient communication is vital for a successful partnership. Choose a supplier that provides excellent customer support and is responsive to inquiries and feedback.
5. References and Case Studies
Review testimonials and case studies from other clients. This can provide insight into the supplier's reliability, quality, and ability to meet deadlines.
The Future of CNC Lathe Machining in Metal Fabrication
The landscape of CNC lathe machining is constantly evolving. Key trends shaping its future include:
1. Automation and AI Integration
With advancements in artificial intelligence and robotics, we see an increasing trend toward automation in CNC machining. This leads to more efficient production lines, reducing labor costs and human error.
2. Sustainability Practices
As industries face increasing pressure to adopt sustainable practices, CNC machining is adapting through recycling materials and minimizing waste during the production process.
3. Customization and Flexibility
There is a growing demand for customized solutions. Future innovations will likely focus on enhancing the flexibility of CNC machines, allowing them to produce small batches of customized parts more efficiently.
4. Enhanced Training and Skill Development
The industry will require skilled operators and programmers proficient in CNC technology and software. Emphasizing training will help meet future demands and technological advancements.
Conclusion
As the manufacturing landscape continues to transform, understanding CNC lathe machining becomes increasingly vital for businesses involved in metal fabrication. Collaborating with a trusted China CNC lathe machining supplier can unlock numerous advantages, from cost savings and technological access to quality assurance and scalability. At deepmould.net, we are committed to staying at the forefront of CNC lathe technology, ensuring our clients receive superior services and products tailored to their needs.
Invest in quality, embrace innovation, and partner with the best in the industry to elevate your business!